How to select and optimize Titanium Dioxide?
Titanium dioxide (TiO2) is the white pigment used to give whiteness and hiding power, also called opacity, to coatings, inks, and plastics. The reason for this is two-fold:
- TiO2 particles of the right size scatter visible light, having wavelength λ ≈ 380 - 700 nm, effectively because TiO2 has a high refractive index
- It is white because it does not absorb visible light
The pigment is expensive, especially when volume prices of systems are used. Most paint and ink companies buy raw materials per weight and sell their products by volume. As TiO2 has a relatively high density, ρ ≈ 4 g/cm3, the raw material contributes substantially to the volume price of a system.
Let’s learn more about this pigment starting with its scattering efficiency…
Scattering by Solid Particles
The refractive index, represented by the letter n, of a material describes how light propagates through, and is bent by, that material. The magnitude of the refractive index, depending upon the electronic structure of the molecules, governs to what extent the path of light changes, when entering or leaving a material.
Particles in a matrix, like pigment particles surrounded by the binder system in a coating, ink or plastic, can change the propagation direction of light when the particles and the matrix have a different refractive index. This phenomenon, called scattering, results in both white color (provided that the particles do not absorb visible light) and hiding power of the system.
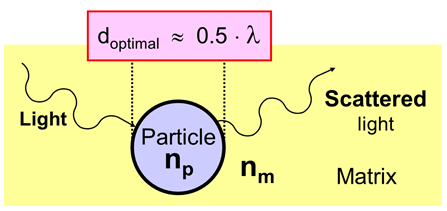
Scattering Efficiency
The scattering efficiency of pigment particles in a system is governed by two key properties.
Scattering is strong when the difference in refractive index of particle & matrix, Δn = np - nm, is big
The refractive index of binders used in coatings and inks is around 1.55. Titanium Dioxide is preferably used as scattering source because the pigment does not absorb visible light and it has a high refractive index.The size of the scattering particles is important
For a specific wavelength of light, λ, there is an optimum with respect to particle size. Particles give maximum scattering efficiency when the diameter of the particles is about half the wavelength of the electromagnetic radiation that is scattered. This implies that particles with a diameter of around 280 nm scatter visible light, with wavelength λ ≈ 380 - 700 nm, most efficiently.Continue reading to master your knowledge in TiO2 pigment, or simply click the specific segment you wish to explore more on:*
Ways to optimize the use of TiO2 in paint and coatings formulations
The 2 crystal structures of TiO2 used for paint & coatings & their photoactivity
Pigment Volume Concentration
The properties of a system, like a coating, are governed by, amongst others, the loading of the system with solid particles. Particle loading is quantified by the property Pigment Volume Concentration (PVC). The PVC of a system is defined as the volume percentage of solid particles in the system after film formation has taken place:
Vp: Total volume of all pigments in the system
Vf: Total volume of all fillers in the system
Vb: Volume of the non-volatile part of the binders in the system
The definition implies that the PVC of a system is calculated by leaving the volatile components, like water and solvents, out. The volumes of the non-volatile components should be used, implying that weights must be transferred into volumes by using the density of each of the components.
A system of high PVC has a high loading of solid particles and a system of low PVC contains a low amount of solid particles, as shown in the figure below:
The TiO2 particles must be separated from each other and distributed uniformly over the system, in order to obtain optimum scattering of each primary titanium dioxide particle.Pigment particles hinder each other with respect to scattering when the particles are close to one another. The PVC of a system, especially the PVC in TiO2, is important with respect to the scattering efficiency of TiO2 particles. The distance between titanium dioxide particles goes down when the PVC in TiO2 goes up.
At PVC in TiO2 of around 15%, the distance between the pigment particles becomes so small that particles start to interfere with each other. The scattering efficiency of each pigment particle becomes worse and worse when the PVC in titanium dioxide is increased between 15 and 30%.
When the PVC in TiO2 is higher than about 30 volume%, the particles interfere so strongly that scattering power goes down when more TiO2 particles are added. This implies that:
Adding titanium dioxide to paint in large quantity worsens both hiding power and
white color strength when raising the PVC in TiO2 above 30%!
With respect to the composition of a system that contains titanium dioxide pigment that is meant to give whiteness and hiding power because of scattering, the PVC in TiO2 should not exceed the threshold value of 30 volume-%. The total PVC, taking all solid particles into account, of a system can be (much) higher than 30%, as long as the PVC in TiO2 is below 30%.
Ways to Optimize the Use of Titanium Dioxide for Paint Industry
Optimize the Dispersion Process
Each primary TiO2 particle has to be used as efficiently as possible. TiO2 pigment scatters light most efficiently when all particles are separated from each and distributed over the system.
A challenge in this respect is that solid particles attract each other strongly. This has two implications:
- A lot of work must be done to separate the particles from each other during the dispersion process. Separation is done by using high-energy dispersion equipment like:
Disk disperser (often called dissolver), or
Pearl mill
The shear forces in a dissolver set-up are too weak to separate all primary pigment particles from one another. More complete separation is obtained by using a pearl mill. - The particles must be stabilized against flocculation. That is, the spontaneous gluing together of solid particles in a liquid caused by the attractive forces between the particles. Stabilization against flocculation is obtained by adsorbing a stabilizer, called dispersant, at the surface of the solid particles immediately after particles have been separated from each other.
The dispersant assures that the particles repel each other. Thus, particles remain separated from each other. Two mechanisms can be used for this:
- Electrostatic stabilization: It results when all particles have an identical electrostatic charge.
- Steric stabilization: It results from polymeric tails, being part of the dispersant molecules, that dissolve in the liquid continuous phase surrounding the particles.
Distribute the Particles
The scattering efficiency of expensive titanium dioxide pigment is maximized when all primary particles are separated from each other, stabilized against flocculation and distributed over the complete system. The distance between the individual pigment particles should be as large as possible. It is said that the pigment particles must be spaced in the system.
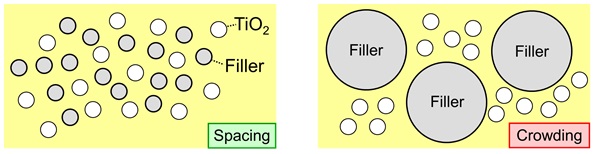
Spacing can be obtained when TiO2 particles are combined with filler particles that have a comparable size. The filler particles do not scatter light but they prevent interference of the titanium dioxide particles. Crowding, the undesired grouping together of TiO2 particles, results when the pigment is combined with filler particles that are big, compared to the TiO2 particles.
Optimum whiteness and hiding power of titanium dioxide pigment can be obtained by combining
the pigment with the right dosage of filler particles with the right size.
Pigment Professionals - Stay Alert!
Reduce costs! Use less titanium dioxide in paint for same performance with an unbiased review of today’s best reduction strategies. Take the online course: TiO2 Optimization: Practical Formulation Strategies today to learn how to achieve best cost/performance ratio while working with TiO2.
Crystal Structures of Titanium Dioxide
Titanium dioxide particles are crystalline. The individual chemical units of titanium dioxide, TiO2, can be stacked in several ways, giving different crystal structures. Mainly two crystal structures of titanium dioxide are used for pigments: anatase and rutile.
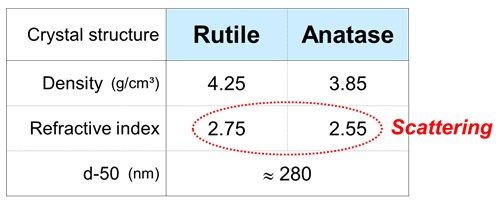
The two crystal structures have an identical chemical composition, but the spatial orientation of the TiO2 units in the crystal lattice differs. Because of this difference, the two materials differ slightly in properties like density, Moh hardness, and refractive index.
The density of titanium dioxide in paint depends on the type and amount of post-treatment. Anatase TiO2 has a lower hardness than rutile, implying that anatase particles are less abrasive and therefore give less wear of equipment. This is beneficial for some applications. Rutile titanium dioxide has the highest scattering efficiency because rutile TiO2 has a higher refractive index than anatase.
Photo Activity of TiO2
Titanium dioxide particles hardly absorb visible light. However, TiO2 particles do absorb UV radiation, for example from sunlight.
Chemical reactions take place at the surface of a TiO2 particle when UV light is absorbed. It is said that titanium dioxide is photoactive. Radicals, chemical substances of high reactivity, are formed when UV radiation is absorbed in the surface of a titanium dioxide particle. The radicals can induce chemical reactions in which the polymers in the system are broken down. This phenomenon is highly undesirable, as it breaks the system down upon exposure to sunlight. Such a system is said to have a poor weathering resistance or that it has a poor outdoor durability.
Post-treatment
Photocatalytic degradation of a system containing titanium dioxide pigment is prevented by post-treating the pigment particles. By doing so, the photoactive TiO2 core of each pigment particle is shielded and photochemical breakdown of the binder system by radicals is prevented.
Alumina (Al2O3), silica (SiO2) and zirconia (ZrO2) are the main inorganic post-treatments used for titanium dioxide pigments. The amount and quality of post-treatment govern how suitable the pigment is to be used for systems, like coatings, inks, and plastics, that are exposed to sunlight.
Depending on the post-treatment, the surface of TiO2 particles can either be dense or porous. Next to inorganic post-treatment, a low percentage of organic material is used in the final steps of the production process of titanium dioxide pigment. The main objective of organic post-treatment, often consisting of alcohols, is to improve the dispersibility of the pigment. An effective organic post-treatment assures that it is easier to separate the primary particles from each other during the dispersion process.
Production of TiO2 Pigment
A few processes are used to produce TiO2 pigment.
- Rutile TiO2 is found in nature. This is because the rutile crystal structure is the thermodynamically stable form of titanium dioxide. In chemical processes natural TiO2 can be purified, thus obtaining synthetic TiO2.
- TiO2 pigment can be made from ores, rich in titanium, that are mined from the earth. Two chemical routes are used to make both rutile and anatase TiO2 pigments.
In the sulfate process, the titanium-rich ore is reacted with sulfuric acid, giving TiOSO4. Pure TiO2 is obtained from TiOSO4 in several steps, going via TiO(OH)2. Depending on the chemistry and route chosen, either rutile or anatase titanium dioxide is made.
In the chloride process, crude titanium-rich starting material is purified by converting titanium to titanium tetrachloride (TiCl4) by using chlorine gas (Cl2). The titanium tetrachloride is then oxidized at high temperature, giving pure rutile titanium dioxide. Anatase TiO2 is not made via the chloride process.
In both processes, the size of the pigment particles as well as the post-treatment is adjusted by fine-tuning the final steps in the chemical route.
Selecting the Right Type of Paint Pigment Titanium Dioxide
The properties and behavior of titanium dioxide, as discussed above, should be taken into consideration when a TiO2 pigment must be chosen.
- A pigment with the right crystal structure should be selected. Rutile TiO2 scatters visible light most efficiently because of the high refractive index: nrutile = 2.75.
- The particles must have the right size. The average primary particle diameter, called d-50, should be around 280 nm for the optimum scattering of visible light.
- The amount and composition of the inorganic post-treatment should be chosen correctly with respect to the application. The type and amount of post-treatment of the pigment govern the degree of photoactivity. For outdoor durable coatings, for example, rutile TiO2 grades with a high percentage of alumina (Al2O3), silica (SiO2) and/or zirconia (ZrO2) should be used.
These three selection criteria can be checked easily as, in general, crystal structure, average particle size and type and amount of inorganic post-treatment can be found in the technical documentation, as provided by the pigment producer.
There are a few attention points that are less easy to check. The particle size distribution (PSD) of the pigment, for example, should be narrow with the maximum at d ≈ 280 nm.
Also, the pigment should contain a low amount of aggregates, primary particles glued or fused together so strongly that they will not be separated when using conventional dispersion equipment, like a dissolver or bead mill. The primary particles should be easy to separate. In technical documentation, this is often referred to as easy dispersible. Both the degree of aggregation and the dispersibility are governed by the production process of the titanium dioxide supplier.
Anatase TiO2 has the disadvantage of scattering visible light less efficiently than rutile TiO2. On the other hand, anatase particles have a lower Moh hardness than rutile particles, implying that anatase gives less abrasion of equipment.
Often titanium dioxide pigments made via the sulfate process tend to be a little bit more yellow than pigments made via the chloride process. In practice, this slight color difference is hardly visible in complete systems.
TiO2 Nanoparticles
In most systems, titanium dioxide in paint industry is used as a white pigment, giving high white color strength as well as hiding power, called opacity.
TiO2 absorbs UV radiation effectively, especially when the pigment particles are small. Small particles have a high specific surface area and are therefore effective in absorbing radiation. Nano-sized post-treated titanium dioxide (nano-TiO2) pigments, with rutile crystal structure and particle diameter of around 10 nm, are used as UV absorber in systems ranging from coatings to sun creams. A coating containing nano-TiO2 is transparent because the particles do hardly scatter visible light.
However, in most coatings UV protection is assured by using organic additives, like UV absorbers in combination with radical scavengers.
Substitute for Titanium Dioxide in Paint
Titanium dioxide in paint industry can be combined with other materials that scatter visible light to obtain extra scattering efficiency. A precondition for such a material is that it has a refractive index that differs substantially from the refractive index of the binder system surrounding the particles. Preferably, it is possible to distribute the material as particles with a diameter of around 300 nm in the system.
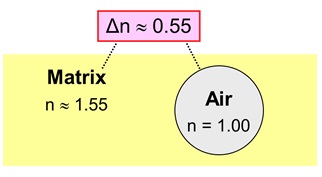
It turns out that there is only one real practical option: the use of air, having a refractive index n = 1.00. Air particles in a system do not absorb visible light and they give both a white color as well as hiding power. Apart from that, stable air particles of the right size can act as effective spacers for the TiO2 particles.
Particle↔Matrix|Δn
–|–:
Rutile TiO2 ↔ Matrix|1.20
Air ↔ Matrix|0.55
Air particles do not scatter visible light as effectively as TiO2 particles, even when air is well distributed in the matrix as particles with the optimum diameter. The reason is that the difference in refractive index of TiO2 and binder matrix is bigger than the difference in refractive index of air and binder matrix.
There are several ways to introduce air particles in a coating.
- An approach that is often used is to load the system with such a high amount of solid particles that there is insufficient binder in the system to cover all the solid particles and to fill the spaces between the solid particles. Then, air voids form during film formation when water and/or solvent evaporates from the system.
- Another option is to use fillers that have air bubbles encapsulated within the particles. Flash-calcined kaolin is a filler that was treated with heat in such a way that closed pores are formed in each solid particle.
- An approach used to assure that stable air particles of the right size are introduced in the system is to use hollow polymeric filler. After film formation, the filler particles consist of an air core in a shell of polymer. The size of the whole particle, as well as the thickness of the shell of each particle, is such that the air within the particles gives optimal light scattering. Apart from this, hollow filler particles of the right size arrange spacing of the pigment particles.
Use the Concepts in Practice
Practice shows that often a lot of money can be saved when titanium dioxide pigment is used to give whiteness and hiding power to a coating, especially by:
- Improving the separation process, and/or
- Changing the type or amount of dispersant
It is worth the effort to study your system and try to find out whether the primary TiO2 particles in your system are: - Separated from each other
- Stabilized sufficiently against flocculation, and
- Distributed well
A possible next step might be to study whether any options are available to introduce or improve spacing of the TiO2 particles in your system.
Commercially Available Grades for Titanium Dioxide for Paints & Coatings
TINOX A-2380 TINOX
TINOX A-2380is a pure, dry-milled anatase universal pigment from the sulphate process. This type of pigment is used in a wide range of applications for instance paints, paper and ceramics, especially where the high whiteness of anatase is desired. TINOX A-2380 provides an excellent brightness and whiteness, strong dispersibility and a neutral undertone. viewmore
Tinox CR-200 TINOX
Tinox CR-200With special surface treatment, CR-200 rutile TiO2 produced by chloride process has high durability, and processing rheology so its dry powder can be easily conveyed. It also has good compatibility and dispersibility in plastic system so is suitable for exterior plastic items. viewmore
Tinox CR-510 TINOX
Tinox CR-510is a rutile universal TiO2 pigment from the chloride process which can be used in paints and coatings as well as in plastics. Produced with advanced technologies, particularly in terms of particle size control, this type of pigment shows excellent optical properties. TINOX CR-510 convinces in the pigmented system by strong hiding power and tinting strength, excellent gloss properties, excellent dispersibility and a blue undertone. CR-510 has an inorganic surface treatment in combination with a special organic post-treatment, which qualifies wide usage in high gloss paints, coatings for sheets, powder paints and polyolefins, PVC, ABS resins. viewmore
Tinox R-2140 TINOX
Tinox R-2140is a rutile universal pigment from the sulphate process for aqueous and solvent-based paint and coating systems. It produces good optical properties in the pigmented system.This pigment is suitable for indoor and outdoor applications.This Ti02 pigment type produces excellent hiding power, good gloss Properties with strong dispersibility. viewmore
Tinox R-2160 TINOX
Tinox R-2160is a rutile universal pigment from the sulphate process for aqueous and solvent-based paint and coating systems. It produces strong optical properties in the pigmented system.This pigment is suitable for indoor and outdoor applications.This Ti02 pigment type produces good hiding power with excellent gloss Properties and excellent dispersibility. viewmore
Tinox R-2180 TINOX
Tinox R-2180is a rutile universal pigment from the sulphate process for aqueous and solvent-based paint and coating systems. It produces excellent optical properties in the pigmented system with a less yellow undertone.This pigment is suitable for indoor and outdoor applications.This Ti02 pigment type produces excellent hiding power with excellent gloss properties with strong and excellent dispersibility. viewmore
Tinox R-2240 TINOX
Tinox R-2240is a sulphate process rutile pigment intended for use in plastics and has an inorganic post-treatment with aluminum and zirconium as well as an organic post-treatment. TINOX R-2240 shows good tinting strength, good hiding power and opacity as well as good dispersing properties and good processibility. viewmore
Tinox R-2280 TINOX
Tinox R-2280is a sulphate process rutile pigment specially designed for the use in plastics. It has an inorganic posttreatment, as well as a very hydrophobic organic posttreatment. TINOX® R-2280 has a blue undertone and excellent properties in opacity and gloss. The unique production process grants R-2280 excellent dispersibility in plastics, low volatile, resistance at high temperatures and excellent processability. TINOX® R-2280 is used in a variety of different plastics. viewmore
How to select and optimize Titanium Dioxide?
https://tio2.info/2019/08/05/Titanium-Dioxide-Optimization-Selection-Strategies/